İngilizce’de “Invesment Casting” , “Ceramic Shell Casting”
(seramik kabuk dökümü) veya “Lost Wax Process” (kaybedilmiş mum
prosesi), Almanca’da “Feinguss” veya “Schalenguss”, Fransızca’da
ise “Fonde a Cire Perdue” ismiyle anılan hassas döküm asırlardan
beri bilinen çok eski bir döküm yöntemidir. Yöntemin günümüzden
3000 yıl önce Mısır’da ve Şang Hanedanı döneminde Çin’de
kullanıldığı bilinmektedir. Hassas döküm tekniğinin prensibi, mum
ve benzer modeller kullanılarak hazırlanan kalıpların ısıtılması
ve eriyen model malzemesinin kalıptan dışarı akıtılarak kalıp
boşluğunun oluşturulmasıdır.
Hassas Döküm Teknikleri:
Hassas döküm teknikleri temelde ikiye ayrılır: “Hassas Kabuk
Döküm” (Investment Shell Casting) tekniğinde, seramik kalıp, ince
cidarlı bir kabuk şeklinde modelin etrafını örterken, “Dereceli
Hassas Döküm”(Investment Flask Casting) tekniğinde ise bir kabın
içindeki kalıp boşluğu haricindeki tüm hacim seramik/alçı malzeme
ile doldurulur:
1-
"Hassas Kabuk Döküm" (Investment Shell Casting):
Bu
cins döküm için yapılan işlemleri kısaca şöyle sıralayabiliriz:
Öncelikle, metalden dökülmesi istenilen parçanın mum veya benzeri
bir malzemeden modeli hazırlanır. Genellikle alüminyum (kuyumculukda
ise
silikon)
bir kalıp imal edilir ve plastik enjeksiyon yöntemi ile
istenildiği kadar mum model elde edilir. (Döküm sonrası soğuma ve
büzülme tahmini yapılarak model aslından biraz büyük imal
edilebilir)
1
2 3
(1)
Parçalar yine mumdan yapılmış bir gövdeye yapıştırılarak "mum
salkım" hazırlanır. Mum malzeme, 70-90 °C arasında olabilen düşük
ergime sıcaklığına sahip ve seramik kabuğu çatlatmaması için düşük
ısıl genleşme özelliğine sahip bir malzemedir.
(2) Model, seramik banyosuna batırılarak (sulu alçı
görünümünde bir sıvı) çevresine ince bir tabaka kaplanması
sağlanır. Seramik tabaka kuruyup katılaşıncaya kadar bir fırında
bekletilir. Yeteri kalınlıkta seramik kaplanıncaya kadar son iki
işlem tekrarlanır. Dış tabakalarda daha kalın seramik tozu
kullanılır.
(3) Dış cidarı sert seramik kaplı parça bir fırına
sokularak modelin eriyip dışarı akması sağlanır. Seramik malzeme
ise yüksek sıcaklığa dayanıklı olduğundan şeklini muafaza eder. Bu
esnada mum modelin akarak çıkmayan kısımları da tamamiyle
buharlaşır. Ardından, fırın sıcaklığı yükseltilerek belli bir süre
içinde seramik kabuk pişirilerek sinterlenir ve sonraki döküm
işlemlerine dayanacak şekilde mukavemetinin artması sağlanır.
4
5 6
(4)
Mum salkımdan kalan boşluğa (daha önce bırakılmış bulunan bir
ağızdan) ergimiş halde metal dökülür.
(5) Metal soğuyup katılaştıktan sonra darbe ile dış
cidardaki seramik kırılarak parça ortaya çıkarılır.
(6) Parçalar ana gövdeden dairesel bir testere ile
kesilerek alınır, bir başka değişle göbek bağları kesilir.
Ardından, gerekli çapak alma, temizleme ve yüzey parlatma
işlemleri yapılır. Son olarak ise kalite kontrol işlemleri
yapılır. Dökümde tahmin edilemeyen boyutsal çekme veya çarpılmalar
varsa bunu kompanse edecek şekilde mum modeller tekrar tasarlanıp
üretilebilir...
2-
"Dereceli Hassas Döküm" (Investment Flask Casting ):
1-
Mum
modeller model ağacına eritilerek yapıştırılır
2- Silindirik bir gömlek (fanus) model ağacı etrafına
geçirilir.
3- Gömlek ile model ağacı arasındaki tüm boşuklara
alçı/seramik karışımı dökülür.
4- Fırında ısıyla karışım kurutulur ve kalıp ters
çevrilerek içindeki mum modellerin eriyip akması sağlanır.
5- Sıcak kalıp ergimiş metal ile doldurulur. Vakum veya
merkezkaç kuvvetiyle döküm kolaylaştırılabilir.
6- Basınçlı su büskürterek kalıp malzemesi temizlenir.
7- Döküm ağacından koparılan parçalar malzeme giriş
çapakları temizlenerek döküm sonrası kullanıma hazır hale
getirilirler.
Uygulama Örnekleri:
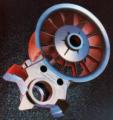 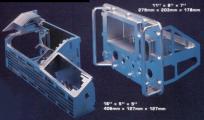 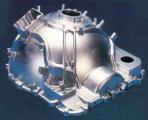
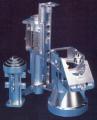 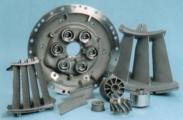 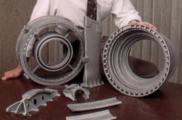
Askeri elektronik cihazların kasaları ve jet türbin parçalarından
örnekler içeren yukarıdaki resimler hassas kabuk döküm ile imal
edilen parçaların ne kadar karmaşık olabileceğini gösteren güzel
örneklerdir.
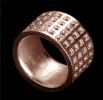
Şekilde gösterilen safhaya gelmiş olan yüzük dökümlerinin
bulunduğu bir hassas döküm ağacı görülmektedir. Mücevher
imalatçıları hassas fanus döküm tekniğini yaygın ve etkili bir
şekilde kullanmaktadırlar.
Modern bir hassas kabuk döküm fabrikası:
1-
2-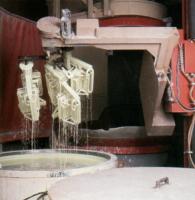
3-
4-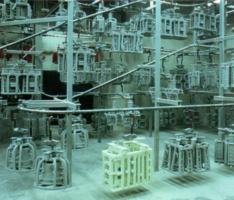
5-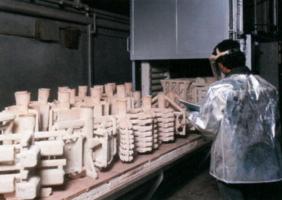
1-
Mum model parçaları kontrolden geçirilip monte edilerek daha
karmaşık modeller oluşturuluyor: Hassas döküm sektöründe sıkça
karşılaşılan karmaşık mum modelleri bir seferde bir enjeksiyon
kalıbıyla üretmenin zorluğu veya imkansızlığı sebebiyle iki veya
daha fazla mum model parçası ayrı enjeksiyon kalıplarında imal
edilir ve manuel olarak birleştirilir.
2- Tam otomatik kabuk üretim hattında robot yardımıyla mum
model üzerine ince seramik kaplanıyor.
3- Kabuğu sağlamlaştırmak için daha kalın seramik (kum)
kaplanıyor.
4- Kabuk oluşturma işlemlerinin ara safhalarında nem ve
sıcaklık kontrollü ortamda kabuklar kurutulurken.
5- Seramik kabukların kür edildiği tünel fırın.
Uygulama Alanları:
Hassas döküm tekniği 2. Dünya Savaşına kadar ticari olarak sadece
kuyumcu ve dişçiler tarafından uygulanmış; daha sonra özellikle
uzay, havacılık ve savunma ,tıbbi ve ortopedik cihaz , otomotiv ve
motor, tekstil, mekanik ve elektromekanik sanayinde hassas
parçalara duyulan ihtiyaç, yöntemin endüstriyel uygulamasını
yaygınlaştırmıştır.
Hassas Dökümün Üstünlükleri:
·
Küçük
ve karmaşık biçimli parçaların üretimi uygundur.
·
Boyut
hassasiyeti ve yüzey kalitesi mükemmeldir.
·
Genellikle ek işlemlere gerek kalmadığından, işlenmesi güç
malzemelerin dökümünde tercih edilir.
·
Kalıp
tek parçalı olduğundan parça yüzeyinde bölüm düzleminin izi
kalmaz.
·
Mum
tekrar tekrar kullanılabilir.
Hassas Dökümün Sınırları:
·
Her
bir parça için ayrı bir modelin üretilmesi gerekir.
·
Yöntem mekanizasyona uygun olmayıp, üretim hızı ve kapasitesi
düşüktür.
·
Model
ile kalıp malzemelerinin pahalı olması ve üretimin çok sayıda
işlem içermesi nedeniyle parça maliyeti yüksektir.
Sadece 5 kg’dan küçük parçaların dökümüne uygundur.
Bu yöntemin videosu
için
tıklayınız |